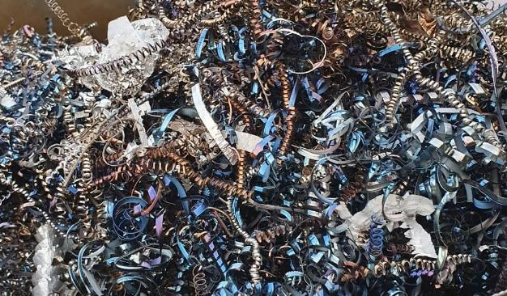
칩=기리꼬=기리빠시=철삭분
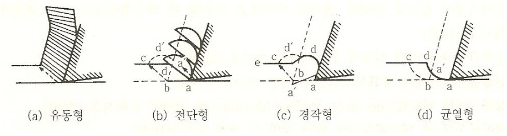
선반, 밀링 등에서 공작물을 깎아낼 때 발생하는 찌꺼기나 철 부스러기는 일반적으로 “기리꼬”나 “기리빠시”로 불리며, 칩 또는 철삭분이라고도 합니다. 바이트를 이용한 가공 과정에서 기리꼬와 기리빠시는 공작면에 닿는 바이트의 가공면에 의해 압축되고, 잘리며, 깎이고, 미끄러지면서 발생합니다. 기리빠시는 가공 방식에 따라 유동형 칩, 전단형 칩, 열단형 칩, 균열형 칩 등으로 구분됩니다.
유동형 칩
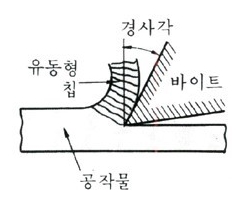
유동형 칩은 기공구 경사면을 따라 연속적으로 발생하며, 전단면이 평면이고 결정 변화가 없는 특징을 가집니다. 가공 중 칩은 공구 경사면을 따라 이동하며, 마찰에 의한 변형 외에는 거의 변형이 발생하지 않습니다. 이로 인해 절삭 저항과 온도에 의한 변형이 매우 낮고, 가공면이 깨끗하게 유지됩니다. 유동형 칩을 발생시키기 위해서는 절삭이 적당히 이루어져야 작업이 용이해집니다. 주로 연성 재료를 큰 공구로, 얕고 고속으로 절삭할 때 유동형 칩이 발생합니다.
전단형 칩
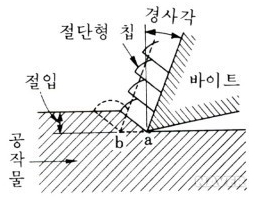
전단형 칩은 공구의 진행에 따라 공작물이 압축되며, 그 압력이 한계에 도달하면 전단이 발생하여 칩이 분리됩니다. 전단형 칩은 주기적인 성질을 가지며, 형태가 변형되다가 변형이 최대에 이를 때 전단면에서 칩이 떨어져 나갑니다. 유동형 칩과 달리 전단형 칩은 이러한 현상이 균일하지 않고, 칩의 형태와 분리 과정에서 변화를 보입니다. 절삭 저항과 온도 변화는 적당한 편이지만, 가공면의 거칠기가 나빠지는 단점이 있습니다. 전단형 칩은 주로 취성 재료를 절삭하거나, 연성 재료를 깊게 절삭하거나 절삭각이 낮을 때 발생합니다.
균열형 칩
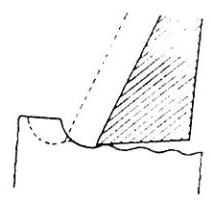
균열형 칩은 백주철과 같이 취성이 큰 재료를 절삭할 때 발생합니다. 이 칩은 절삭력이 가해져도 거의 변형되지 않다가, 한계 압력을 초과하면 순간적으로 균열이 발생하면서 생성됩니다. 균열형 칩은 절삭 저항의 변동이 크며, 균열 파괴에 의해 절삭면이 형성되기 때문에 가공된 면이 깨끗하지 않습니다. 또한, 공구 끝에서 심한 마모가 발생하는 특징이 있습니다.
열단형 칩
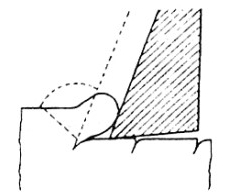
열단형 칩은 매우 연성인 재료를 절삭할 때 발생합니다. 가공이 진행됨에 따라, 공구의 진행선 아래쪽에서 칩이 찢어지듯이 형성되며, 마무리면에 뜯어낸 듯한 자국이 남게 됩니다. 이는 공작물의 점성으로 인해 칩이 공구 경사면에 눌러붙어 유동하지 않기 때문에 발생하는 현상입니다. 이 과정에서는 진동이 발생하며, 가공 상태가 좋지 않고, 불안정한 가공 조건을 나타냅니다. 연성이 매우 큰 재료에서, 공구 경사면과의 마찰이 심해 칩이 공구에 응착하기 쉬운 조건에서 주로 발생합니다.
칩의 종류가 다른 원인
칩의 종류가 다르게 발생하는 원인에는 절삭 조건이 중요한 역할을 합니다. 공작물의 재질은 칩의 종류에 큰 영향을 미칩니다. 예를 들어, 연강처럼 인성이 있는 재료는 유동형 칩이 생성되기 쉽고, 반면 납과 같이 점성이 큰 재료는 열단형 칩이 발생합니다. 주철은 취성이 강해 전단형 칩이 발생하며, 절삭 속도를 늦추고 공구의 경사각을 낮추면 균열형 칩이 발생합니다.
절삭 조건에 따라 칩의 종류가 달라지는데, 절삭 깊이가 낮고 경사각이 큰 공구로 가공하면 유동형 칩이 발생하며, 절삭 깊이가 크고 경사각이 낮은 공구를 사용하면 열단형 칩이 발생합니다.
이처럼 공작물의 재질, 절삭 속도, 절삭 깊이, 공구의 형태, 그리고 칩과 공구의 경사면에서 발생하는 마찰 등이 각기 다른 종류의 칩을 형성합니다. 따라서 가공 시 이러한 요소들을 숙지하고 상황에 맞는 절삭 조건을 설정하는 것이 매우 중요합니다.